Sustainability Snippets
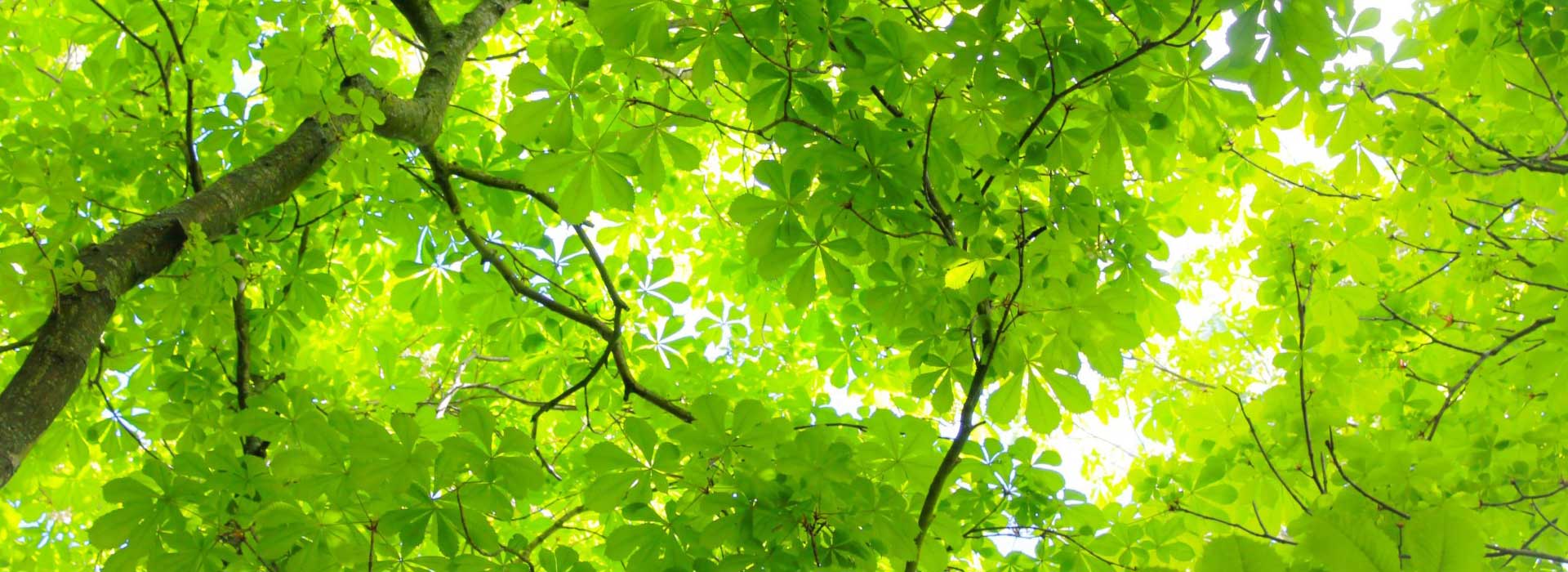
Sustainability Snippets
As part of our sustainability goals and focus on continuously improving our processes, we want to share our knowledge through educational content once a month. Follow us on our journey to a fact-based approach to sustainability.
Carbon neutrality is defined by a state where carbon emissions related to an activity are compensated by funding an equivalent in carbon savings elsewhere.
At Formica Group, reducing our carbon footprint is based on our core belief that it is the right thing to do. We are also convinced that reducing our overall environmental footprint is essential to the long-term success of our business and our environment. We aim to identify the drivers of sustainability and prioritize initiatives across the entire value chain – from raw materials through to consumers’ use of our products.
Efficiency upgrades are one of the first levers for improving a product’s environmental footprint since they reduce energy requirements and raw material inputs. Many opportunities exist to improve the energy efficiency of industrial equipment through the use of modern technology and intelligent system design. Replacing motors and pumps with new high-efficiency designs, storing and recycling heat within a closed-loop system, and optimizing the integrated manufacturing system are examples to reduce energy consumption.
At Formica Group, our goal is to increase process efficiency to reduce our overall energy consumption. Since 2019, we’ve implemented projects at our two manufacturing plants (Cincinnati, Ohio, and St-Jean-sur-Richelieu, Quebec) to increase the efficiency of our process. For instance, we use closed loop systems and optimal recycling of thermal energy across our process. In 2022, the total environmental impact of Formica Group North America’s panels emitted 31% less CO2 compared to baseline year (2019) emissions.
Changing a product’s raw materials usually involves replacing non-renewable inputs. Indeed, choosing materials from renewable sources leads to a reduction of CO2 emissions. For example, in industries such as packaging, environmental issues have driven the need for a shift in materials. Concerns about plastic pollution have led consumers to demand more environmentally friendly alternatives. In turn, this process has driven a rise in the use of biopolymers and biodegradable polymers, which are designed to replace traditional, petroleum-based plastics.
Source : How the manufacturing industry can minimize its carbon footprint (thefabricator.com)
At Formica Group, a large share of industrial emissions is associated with the creation of materials used in our products. A key opportunity exists to minimize material waste at each step in the process. Therefore, we are focusing on product and process designs that optimize the use of materials so that our finished product delivers outstanding performance while requiring less material input. Replacing the most impactful inputs normally translates into switching from fossil-based to bio-based and renewable options; however, it can also mean other things. Since 2019, we have focused on optimizing the use of raw materials through improvements in material yield, internal recycling, and revised product construction requiring less input materials.
Transparency is one of the key components consumers use to compare products and company initiatives. It’s important to consider the information, ask questions and only trust solid data.
At Formica Group North America, we consider transparency in our processes to be just as important as sustainability. That’s why we publish our Sustainability Position Paper annually to share our sustainability intentions with the public. For additional information, visit this web page www.formica.com/sustainability
The LCA, or life cycle assessment, methodology represents the most reliable and data-driven tool available to help companies, institutions, and governments systematically incorporate sustainability into their decision-making process. This method can evaluate the ecological burden related to the entire life cycle of a product, a process, or an activity. The LCA encapsulates the entire environmental footprint from raw material extraction to the disposal stage.
By using a product life-cycle approach, we get a clear understanding of the actual impact we have on the environment. We can then identify the drivers of sustainability and prioritize initiatives across the entire value chain – from raw materials through the consumer’s use of the product. Formica Group North America’s LCA assessment details results tied to three key environmental factors: global warming (CO2 emissions), primary energy demand, and water footprint.
A company can use different scopes when performing a life cycle assessment (LCA) of one of their products, processes, or activities. Cradle-to-gate is an assessment of a partial product life cycle from resource extraction (cradle) to the factory gate (i.e., before it is transported to the consumer).
Cradle-to-grave is an assessment of the full product life cycle from resource extraction (cradle) through to the use phase and disposal phase (grave).
Gate-to-gate focuses only on a product’s manufacturing process.
At Formica Group North America, we use the cradle-to-gate scope for our on-site life cycle assessments (LCAs) because we focus on the stages that are under our control and that we can influence. We can improve our processes to make them more efficient, and we can select less impactful raw materials. Moreover, for the life cycle stages beyond our factory gate, we have limited visibility and data as to the useful life and ultimate disposal of our products. We continue to closely monitor developing regulations on the potential for carbon storage benefits of long life cycle products at the end of their useful life.